Embracing automation – 3 small strategies for big success
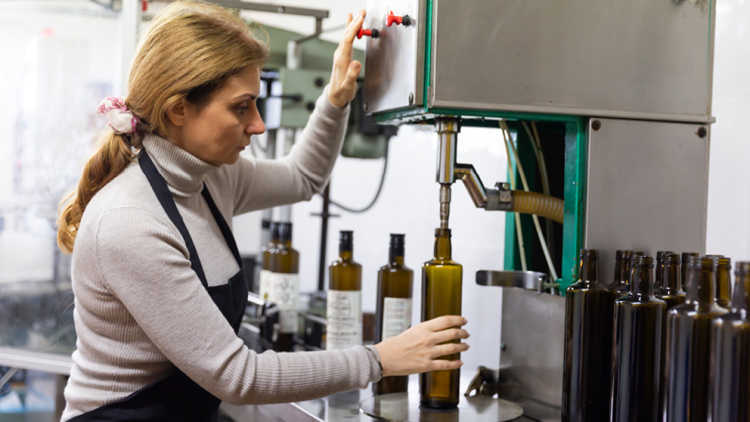
Food processing in Canada is rapidly transforming as businesses aim to achieve or improve productivity with a reduced labour force.
“There's a finite pool of labour moving forward for medium-size manufacturing businesses,” says Frank Luengo, the chief operating officer at Sonora Foods, a tortilla company based in Ontario.
These vacant positions can be particularly tough to fill in less densely populated areas of the country, like the Atlantic provinces, since new Canadians and migrant workers tend to gravitate towards the larger Canadian cities.
“We have between a 40 to 60% turnover each year,” says Russ Mallard, the president of Atlantic Beef Products, a beef processor located in Albany, P.E.I. “So, we’re constantly needing new people.”
With a lack of available employees, food and beverage processors are turning to automation.
With a lack of available employees, Canada’s food and beverage processing companies are forced to consider alternate solutions, which could include automation. Yet automation doesn’t need to be big, expensive and costly. It’s possible to make small changes around your processing facility that will help increase efficiency when labour issues are challenging.
Here are three strategies to consider when putting small-scale automation to work in your food or beverage processing operation.
1. Automate small things for big wins
Automation doesn’t need to be a large, expensive, long-term project. It can mean something as small as making operations more efficient by automating processes; the key is finding a solution that will have the highest positive impact with minimal disruption.
Converting paper-based processes — such as record keeping, accounting or payroll — to digital solutions is often the first entry into automation. These solutions can improve production efficiency, reduce errors, improve traceability and minimize waste. In addition, providing employees with the opportunity to train in these new skill sets can positively impact morale.
"Integrating these digital tools not only makes the employees' work a bit easier, but it also helps them to feel that they are part of something bigger,” Luengo says.
Technological advances also allow food processors to shift their operations away from manual, labour-intensive processes. Small steps after paper-based record keeping could include repetitive tasks such as packaging and labelling the food products or ingredient tote deliveries around the processing floor. However, for these solutions to be sustainable, they must respond to the company’s and its employees’ needs.
2. Employees first, then automation
Automation has been widely adopted at Sonora Foods, with 80% of their production lines using some form of automation.
Luengo stresses that for automation to be an effective solution, companies must invest in the employees first. Developing a solid employee culture can help improve retention while also helping ensure that the chosen solutions align with the employees' needs.
“The most advanced technology and equipment in the world will not run if the person running it doesn’t want it to or had a bad day,” says Garnet Lasby, president of Massilly North America, an Ontario-based manufacturer of metal closures for food jars. “So ultimately, the engagement of employees is what takes that excellent investment of equipment and turns it into excellent productivity on output.
3. Customize and prioritize
Retrofitting existing operations is an option for larger automated processes but can quickly become cost prohibitive. Whenever space and budget allow, leave room to grow into future automation when expanding or building from scratch.
When Atlantic Beef Products extended its business to include value-added products, it began wielding an addition exclusively for processing these products.
However, despite automated solutions for several repetitive manual processes, the challenge was determining which solution to invest in first. For your business, priorities may be determined by which areas have the largest labour needs now or in the future, and the solution should be customized to meet your needs.
Article by: Anne-Marie Hardie