Watch for fixed production costs when increasing acres
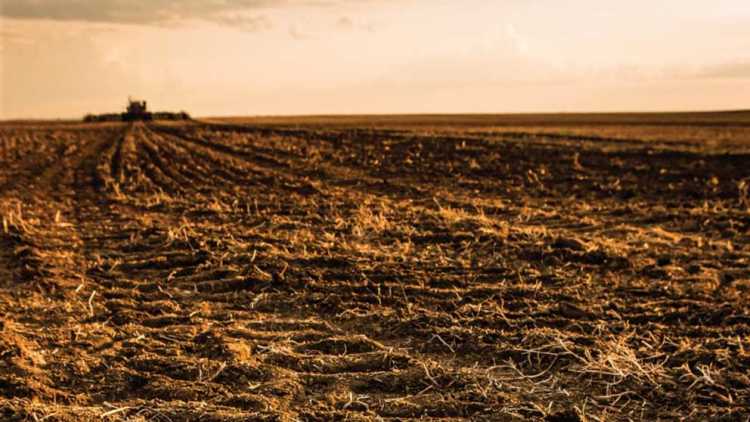
An expansion of your seeded acreage can create more problems than anticipated. If not managed properly, relatively small expansions can decrease a farm’s profitability.
“All too often the extra land creates a time crunch at seeding and/or harvest. If yields are reduced, it will increase the cost of producing each bushel.”
On paper, it can look good. You expand your grain farm by renting or buying additional land. You anticipate farming the extra land without having to upgrade equipment. Spreading your fixed costs over more acres lowers your cost per acre. Presto, you’re more efficient.
It’s a good theory and it can work, but all too often the extra land creates a time crunch at seeding and/or harvest. If yields are reduced, it will increase the cost of producing each bushel.
Know your sweet spot
When Hebert Grain Ventures at Fairlight, Sask., grew to 12,000 acres, managing partner Kristjan Hebert readily admitted the operation was more cost efficient at 8,000 acres. At that size, one large 80-foot seed drill running 24 hours a day could handle the seeding, and two large combines could handle harvest operations.
“Moving from 8,000 to 12,000 acres was tough,” Hebert says. “We feel we need to get to 16,000 acres to be back in a sweet spot for efficiency.”
Hebert says adding incremental harvesting capacity is relatively easy with custom combiners. Seeding can be tougher to outsource, and buying a second smaller seed drill is typically more costly per foot of drill once you consider the cost of the tank and the tractor.
“The human side is even worse than the equipment to scale up,” says Hebert, who has a background in farm financial management. “Good people are vital.” He estimates that in his operation, one full-time person is required for each additional 2,000 acres. Hebert prefers to have people in place and then scale up, versus scaling up and then scrambling for people.
While there are sweet spots in the size continuum, Hebert believes the managers who focus on profit maximization and constant improvement will be the most efficient at any size.
“Better is better, before bigger is better,” Hebert says.
Analysts agree
Agricultural economist Bill Brown from the University of Saskatchewan has evaluated costs for many grain farms over the years, and his conclusions are similar. Economies of size, says Brown, are “lumpy.”
He notes that small- to medium-sized grain farms can run older and smaller equipment and be cost-efficient. As you reach the maximum that can be accomplished with the largest equipment available, further expansion can be more problematic.
Certain sizes are more efficient. The increment varies from one region to the next depending on the length of the growing season, crop yields and the crop mix.
“We wrestle all the time with matching capital assets to the size of the operation,” says Jonathan Small, a farm management consultant with the accounting and financial management firm MNP in Red Deer, Alta. Rather than equipment cost ramping up in lockstep with seeded acres, Small says it more often steps up like a stairway.
“Some producers embark on expansion without a strategy for how to grow,” Small notes. “Some upgrade equipment, but they don’t have a plan for acquiring more land. This can lead to some horrible inefficiency.”
Renting land is often viewed as a way to make money so a farm can eventually purchase land. This won’t work as well as intended if the rented land actually reduces farm efficiency.
There are no magic answers, but it’s important to monitor your equipment investment per acre. You also need to be realistic about how you plan to handle the machinery and labour requirements that will come from an acreage increase.
For more tips on farm size, efficiency and profitability, see:
What’s your annual equipment cost per acre?
Jonathan Small of MNP sees a huge variation in equipment investment per acre from one farm to another. He believes $350 per acre is now typical in Alberta, but he sees producers doing well with only $200 an acre invested in equipment. And he sees other producers who have investment of well over $800 an acre.
While the numbers will be different in each region of the country, the wide variation between farms likely exists everywhere.
As a rule of thumb, Small says you can take 25 per cent of your equipment investment per acre and assume that’s your annual cost. The 25 per cent accounts for annual machinery depreciation of 15 to 20 per cent, five per cent for repairs and an allowance for the cost of money.
For this calculation, leased equipment should be included at fair market value. Depreciation is a “paper” cost on equipment you own until it’s time to sell it. On leased equipment, the cost of depreciation is built into the lease payment.
Kristjan Hebert of Hebert Grain Ventures doesn’t typically buy or lease brand new equipment, believing that tractors and combines with a few hours on them are a better value and help reduce the cost per acre. He advocates careful analysis to see which deals are beneficial to a farm.
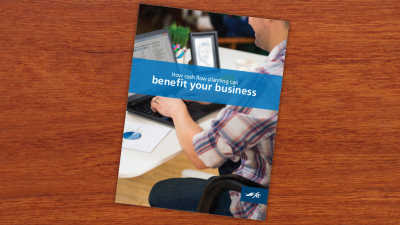
Learn how cash flow planning can keep you on the right financial track.