Seed cleaning: A basic introduction
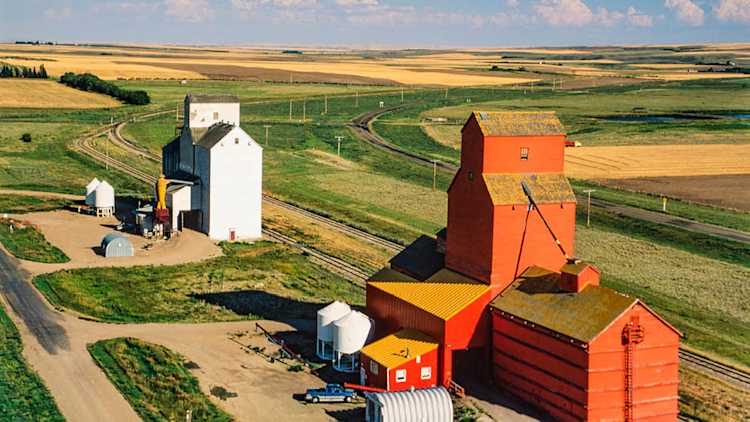
No tiny toothbrush or soap is required. So, let’s talk about seed cleaning!
The what and the why
Wooden elevators that often double as seed cleaners have been a common sight in every small town in the prairies for decades. While those may no longer be the standard, the fundamentals are the same.
Seed cleaning is performed to decrease bulk for shipping, remove seeds with imperfections, and remove any other unwanted seeds or diseases. The end use of the seeds will determine the level of cleaning required. Cleaning for export does not need to be as precise, as there will be an allowance for impurities. Cleaning for food processing will likely need a higher level of cleaning.
For example, wheat for flour manufacturing needs to be nearly perfect and eliminate allergens such as soy. The level of cleaning to plant the next crop can also vary depending on customer specifications.
Traditional seed cleaning is done through several stages:
Screens: Much like a sieve, the screen allows smaller matter to pass while larger matter, such as chaff, is removed.
Indent: Seeds will get stuck in the indents of a horizontal cylinder. The indents will only pick up certain sizes. As the cylinder rotates, the longer seeds will fall out first. Shorter seeds will take longer to fall out and be collected in a separate trough. There may be variations in the process, but the basic concept is the same.
Source: FCC
Gravity table: A sloped vibrating table. Seeds are separated based on density. With vibration and air, the heavier seeds will flow through gates, and lighter seeds will rise to the top and flow out the back.
Colour sorter: Material passes through the machine where cameras, sensors, or lasers will recognize and instantly remove discoloured or broken seeds, often with air.
Types of facilities and who runs them
The highest concentration of these services can be found on the prairies. Most of the cultivated acres in the country are in the prairies, so it makes sense. However, there are facilities nearly everywhere you may find cultivated acres.
The ownership of these facilities varies. Small on-farm operations clean their seed and a couple of neighbours' seeds. There are also seed-cleaning cooperatives. This is typically a group of producers getting together and running a facility. They will often have rail access to avoid trucking in and out. Some of these co-ops can even own a portion of the rail line. These smaller facilities are often cleaning to prepare seed for next year’s crop or to save on cleaning costs. New co-ops are emerging less frequently. The industry istrending to large commercial operations enjoying economies of scale.
The larger commercially licensed facilities differ from the east to the west of Canada. In the prairies, a typical facility will be on the rail line, with exceptions. Some specialty facilities may have to truck in and truck out as well. For the facilities on a rail line, the product is trucked in, cleaned, and loaded onto rail cars for export. These facilities are not always owned locally. Out-of-province or out-of-country investors are often involved.
In the eastern parts of Canada, the facilities are usually smaller. This is related to the number of cultivated acres available in the East. The product is trucked in and cleaned. It is then trucked out to be taken to port or another destination. Commercial operations in both parts of the country can often trade in down years due to inadequate margins for investors.
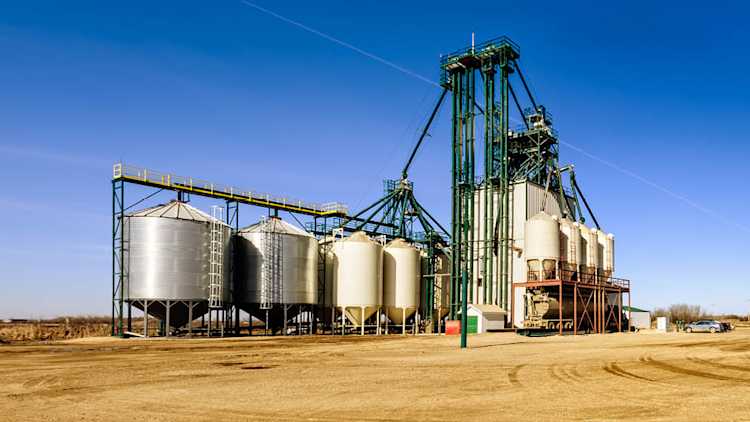
Recent years have also seen some more mobile seed-cleaning plants. It is a time saver as many producers have livestock, maintenance, and other duties. Eliminating an extra trip is beneficial if your cleaner is not on rail or you plan to reuse your seed. A trailer would be outfitted with the necessary equipment, and the product could be taken directly from the producer’s bin, cleaned, and then transferred to an empty bin on site.
Challenges
One of the biggest challenges facing seed cleaners is sourcing seeds. They rely on a good crop year as much as the producers do. A drought or weather event can severely impact the business if there is no product to clean. While producers might have crop insurance, seed cleaners do not. They are dependent on a good growing season.
Disease in the product can be an issue. Equipment needs to be cleaned to prevent the spread of disease. This is especially true of a mobile operation that goes from farm to farm.
There are several methods of packaging as well. Rail cars, sea cans or bagging are the main three. The ability to package the product to meet the market demands is important.
Some challenges are completely out of the operator's control. Sanctions, bans, and availability of rail cars can impact the operation. If the export-grade seed cannot be shipped, they must stop taking new seed once full.
Innovations
Little new technology can be found in the industry.The existing methods have recently been improved. There is some difficulty incorporating them into existing cleaning lines, but the new operations are becoming more automated. Almost any seed type can be cleaned on one line. Switching between seeds is no longer labour-intensive. The same can be said for monitoring. It can be automated, with employees receiving alarms and notifications on their phones. The bagging lines are also becoming more automated with robot bagging and palletization, reducing labour costs.
UV light disinfecting has some benefits that could potentially be incorporated in the future. The food processing industry has used this technology for a while. UV light can reduce bacteria and fungi while potentially increasing germination rates. Installation and operating costs could be minimal. This is more likely to be used in seed treatment than seed cleaning, but it is still noteworthy.
Part of the process
Seed cleaning may be new to you, but you can be sure that when you look in your cereal bowl, the grain you are eating has been through one of these facilities. Just one more step on your food’s journey from the soil to your home.
Article by: Kurri Carlson, Business Intelligence Analyst